QT100 / AR400 / AR450 / AR500 / AR550
For every industrial application, we offer hardened steel plates or parts, designed to withstand intense wear and demanding environments. Thanks to our selection of water- and oil-quenched materials, you benefit from strength optimized to your specific requirements.
The wear resistance of non-particle-reinforced steel depends directly on its hardness: the higher the hardness, the more limited the abrasion. However, beyond a certain threshold, brittleness and other mechanical constraints impose practical limits.
This is where our alternative materials come into their own, offering superior performance without compromising overall strength. Our range of quenched steel comes in three main families, each designed to meet specific conditions of use:
QT (Quenched and Tempered): Water-quenched and tempered, these steels offer an excellent balance between mechanical strength and formability. For example, a QT100 steel has a yield strength of 689 MPa (100,000 psi) and a hardness of around 280 BHN, making it a reliable option for equipment frames, lifting arms or load-bearing structures.
AR (Abrasion Resistant): Richer in carbon, these steels are heat-treated to hardnesses from 400 to over 500 BHN. They are designed to withstand severe abrasion and frequent impacts, particularly in buckets, hoppers, conveyors, container walls and other wear parts.
Dynamic 500: Our oil-hardened AR550 achieves an initial hardness of 470 BHN, rising to 550 BHN under repeated impact. This surface hardening, combined with a tougher internal structure, significantly extends service life. Similar behavior is achieved with oil-hardened AR500, enriched with titanium carbide (Dynamique 500 Plus), particularly effective in pure wear environments without impact.
To assess actual abrasion resistance, we use the standardized ASTM G65-04 Procedure A method, based on the action of a rubber wheel and a dry abrasive (Ottawa sand). However, the natural grain size of the sand may vary slightly from one batch to another, affecting the results. This is why all comparative tests must be carried out in the same laboratory, using a constant batch of sand. The illustration below shows the principle of the testing device, together with a used sample.
Before each series of tests, a standard D2 steel sample is used for verification. Depending on the version of the standard used (ASTM G65-04 or G65-16), the expected lost mass varies as follows:
Key points:
Material: D2 tool steel (recommended hardness: 60±1 Rc)
Nominal target: mass loss approx. 0.20 g
Procedure A: most severe test (130 N load)
The ASTM G65-16 version introduces an additional tolerance of ±16%, on top of the ±3% already present in the 2004 version. This increased inaccuracy makes the test less reliable, especially for highly wear-resistant materials.
In the case of carbide coatings, where losses are extremely low, the use of recent standards can mask critical differences between two high-performance materials. Before any comparison is made, it is essential to check the version of the standard used. Without this rigor, the results may be misleading.
The table below shows the gains in service life observed in ASTM G65-04 tests (procedure A), compared with standard structural steel type 50W (350W):
Our tests and field feedback confirm that these results faithfully reflect the performance observed in real-life conditions.
Plate specifications
Available thicknesses : 3/16″ to 3.0″
Most popular sizes : 48"x96", 96"x96", 96"x120", 96"x144", 96"x240", 96"x288"
(Other dimensions available on request)
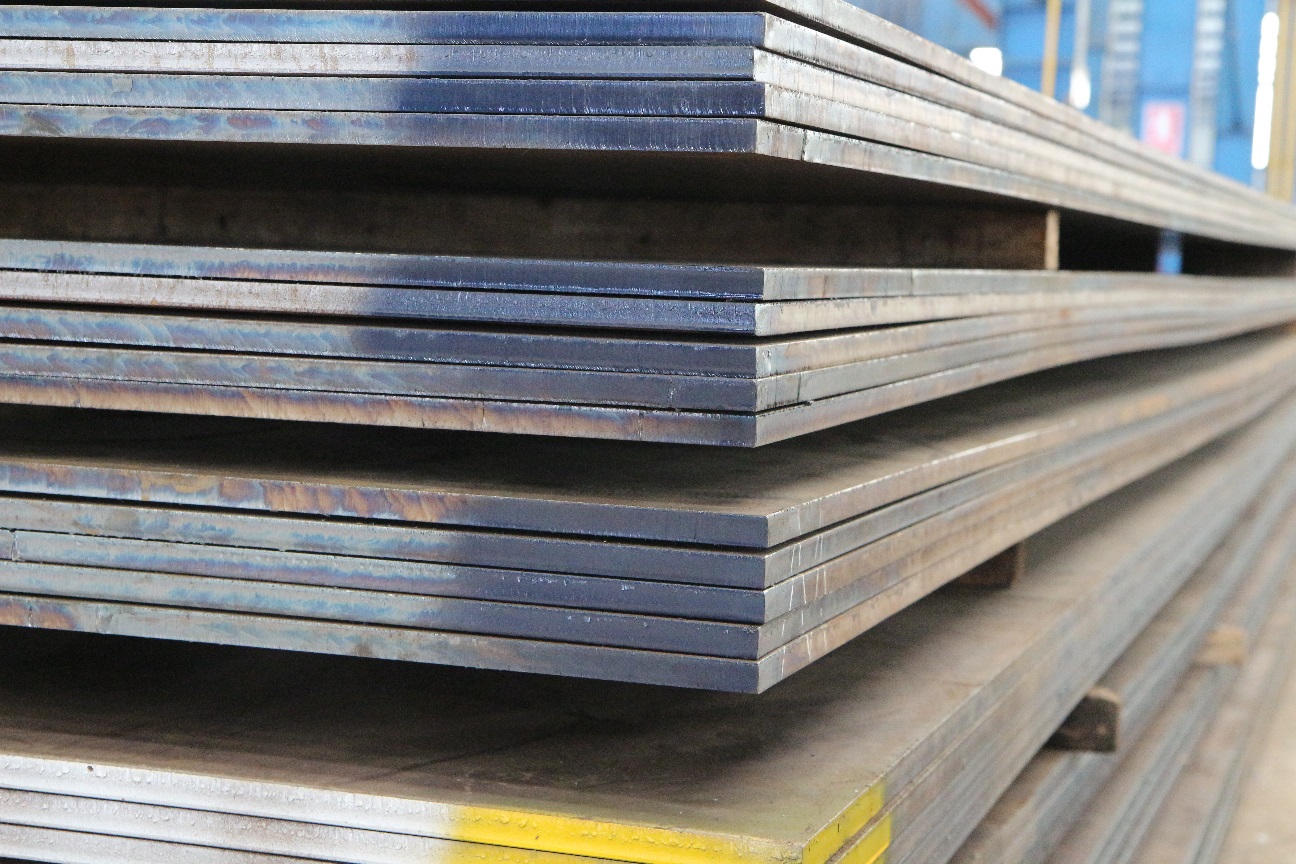
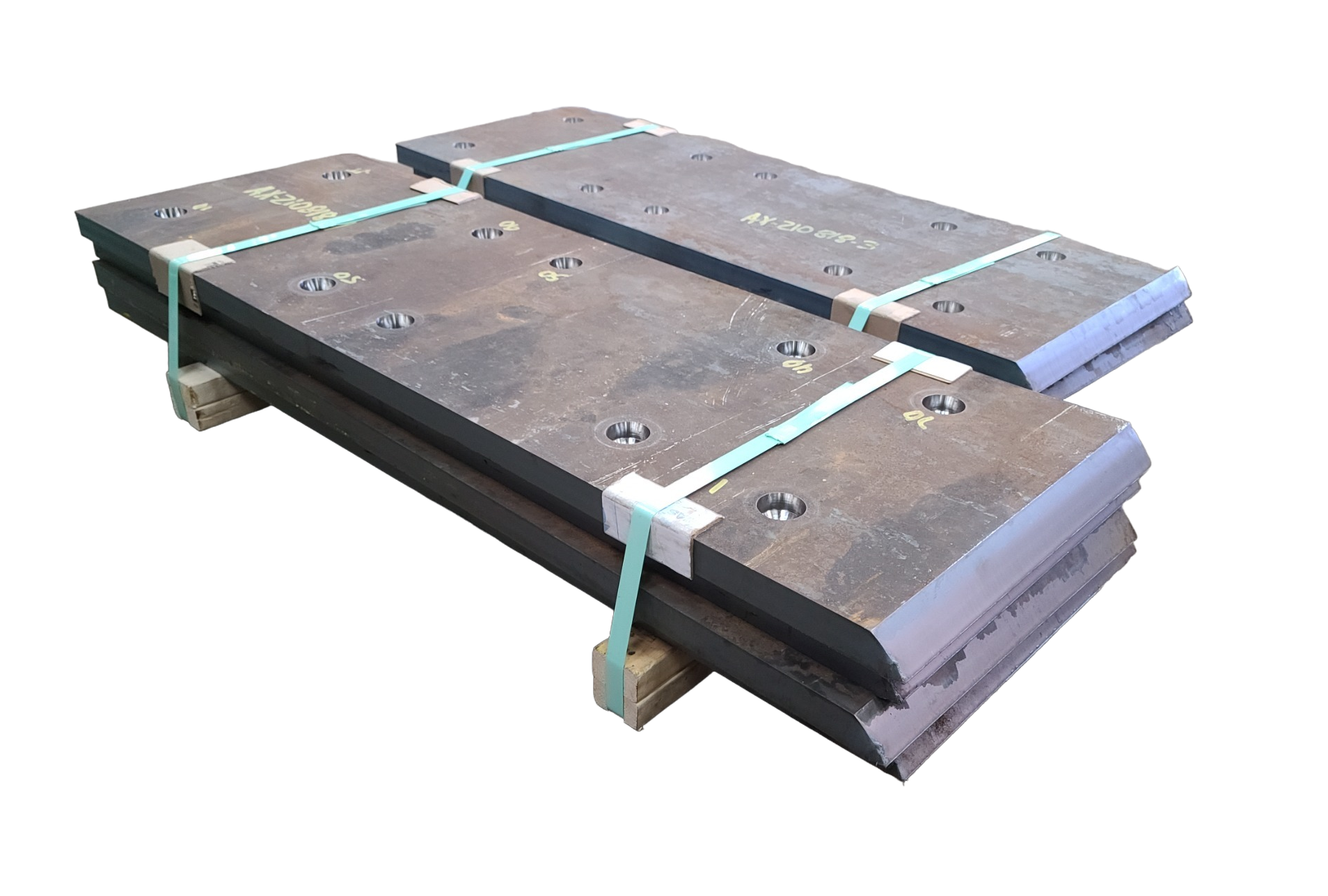
Turnkey parts
Save time, reduce material waste and simplify your logistics with our turnkey service. We cut, form and machine hard steel up to 550BHN with fast turnaround times and rigorous quality control.